Compiled by Bill Meier
31 December 2008
Paul Greaves comments:
Some explanations about casting pinholes:
Pinhole casting |
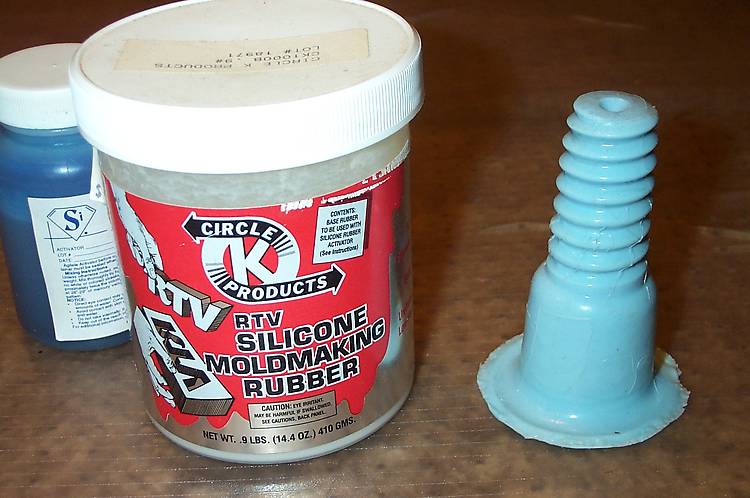 |
This is the material I used to make a casting of the pinhole of an EC&M. It is an RTV silicone mold-making material. |
Pinhole casting |
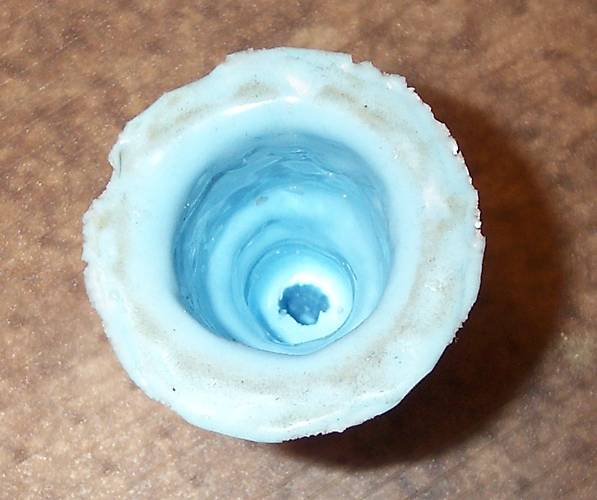 |
This view shows the interior of the casting. As you can see, it is hollow. I did this to make it easier to remove. The material is fairly runny, so it made it difficult to coat the interior evenly. I rotated the insulator to allow the material to coat the interior. Repeating this process as the material starts to set up helped. Still, there was residual that ran down and filled the bottom of the pinhole solid. This made the bottom part difficult to remove. The upper parts were easy, as the walls of the casting are very flexible. I cut a small hole in the middle of the very bottom to facilitate removal. (This material can tear if pulled on too much.) |
Pinhole casting |
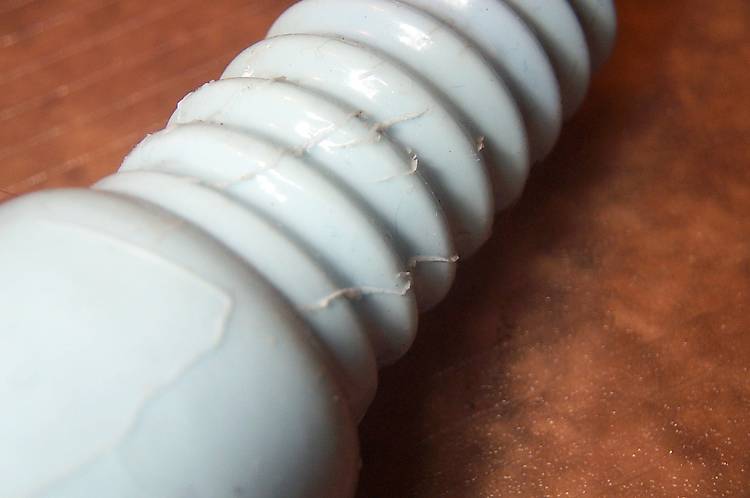 |
This picture shows why these interior castings can be difficult to remove. The interior of the insulator often contains irregularities like bubbles and annealing lines created by the original glass molding process. Since these become filled with the mold making material when attempting a pinhole casting, they serve to "lock in" the casting. In this case, you can see the raised lines caused by the all-to-common shallow cracks (annealing lines?) found in EC&M pinholes. Other older insulators commonly exhibit similar features that could cause difficulties. Newer stuff like Whitall Tatums would probably be less of a problem.
For this reason, I would strongly suggest using a flexible material for pinhole castings! |
Return to the ICON articles page
|